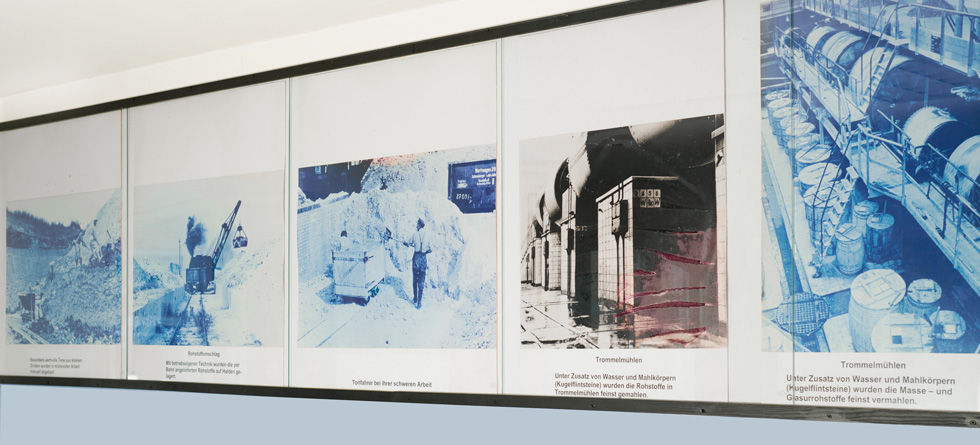
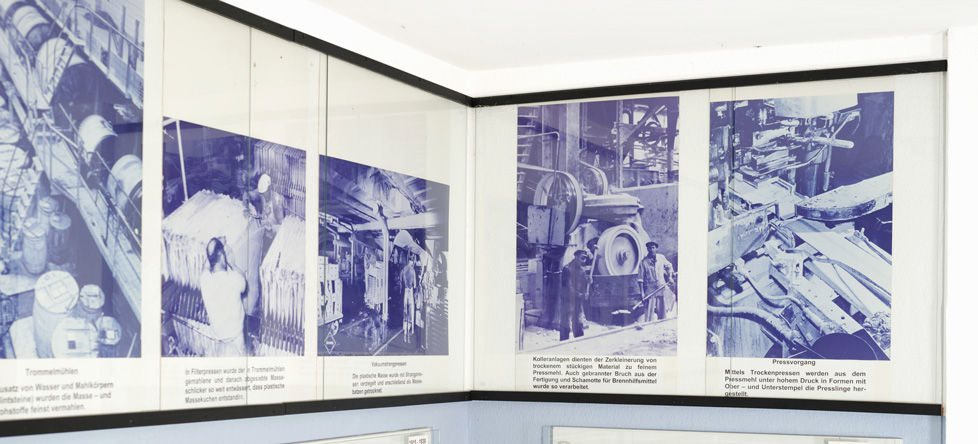

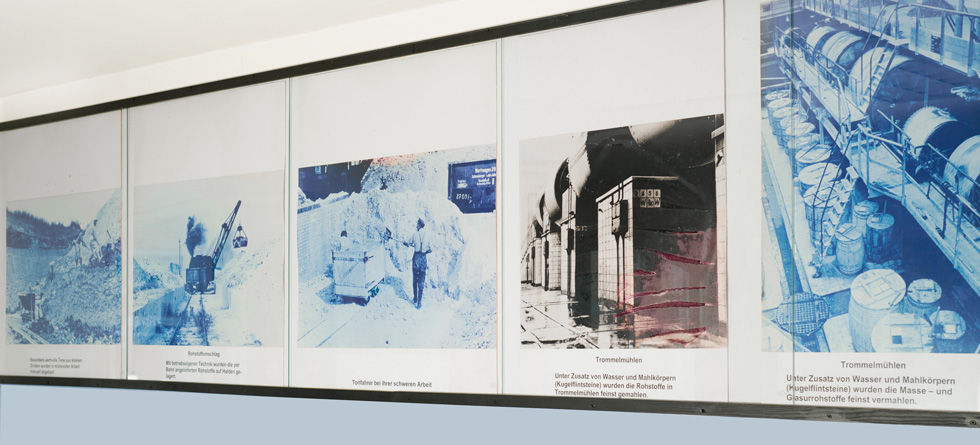
Die Herstellung der Scherben
Für die industrielle Herstellung der Fliesen wurden große Mengen an mineralischen Rohstoffen und viel Energie benötigt. Zunächst aus England und später auch aus Sachsen kamen sowohl die Kohlen für die Öfen als auch die verschiedenen „Erden“ für die Fliesenherstellung per Schiff in den Boizenburger Hafen. Die Gleise der 1889 eingeweihten Boizenburger Stadtbahn, vom Hafen zum Bahnhof, waren schnell mit einer Weiche an das neue Fabrikgelände angeschlossen worden. Die Werksbahn brachte nun das Material vom Hafen ins Werk, ein Kran entlud die Erden in verschiedene Halden – auch Hocks genannt. Dort sollten sie mindestens ein Jahr lang lagern, damit die Brocken schon einmal durch Frost aufgebrochen wurden. Die Tonfahrer füllten dann nach Rezept die passenden Mengen der Erden mit ihrer Schaufel in eine Lore. Aus der Lore wurde die Mischung in ebenerdige Rührbottiche abgelassen, mit Wasser versetzt, maschinell gerührt und gesiebt, bis eine milchige Masse entstand. Diese wurde in die Trommelmühle gepumpt. Sogenannte Kugelflintsteine, die zumeist an der Ostsee gesammelt wurden, übernahmen in der Trommelmühle die weitere „Feinarbeit“, so dass die jetzt entstandene flüssige Masse in die Filterpressen gefüllt werden konnte. In über Holzrahmen gespannten Leinentüchern wurde der Masse durch Pressen die Feuchtigkeit entzogen. Die entstandenen Massekuchen wurden zu Strängen gepresst, dann zu Blöcken geschnitten und - meist zwischen den Tunnelöfen – getrocknet. Schwere körperliche Arbeit, verbunden mit viel Staub und großen Temperaturschwankungen. Die Blöcke wurden in der Kolleranlage anschließend wieder grob zerkleinert und in einer Feinmühle zu Pressmehl verarbeitet. Hieraus wurden die Rohlinge gepresst und mit einer Kennung des Herstellers auf der Rückseite versehen. Die Rohlinge wurden in hitzefeste Kassetten einsortiert und zum ersten Schrühbrand in den Tunnelofen gefahren. Der einmal gebrannte Fliesenrohling wird Bisquit-Scherben genannt. Auf diesen wurde, anfangs per Hand, später durch Tauchen, Sprühen oder Gießen - die Glasur aufgebracht. Es folgte ein zweiter und abschließender Brand, bevor die fertige Fliese verpackt und über den Boizenburger Hafen in alle Welt verschifft werden konnte.
Mehr Erfahren
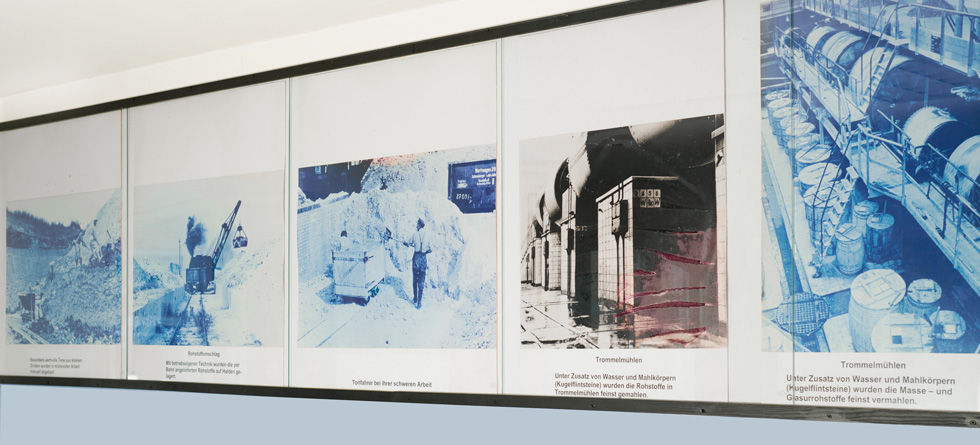
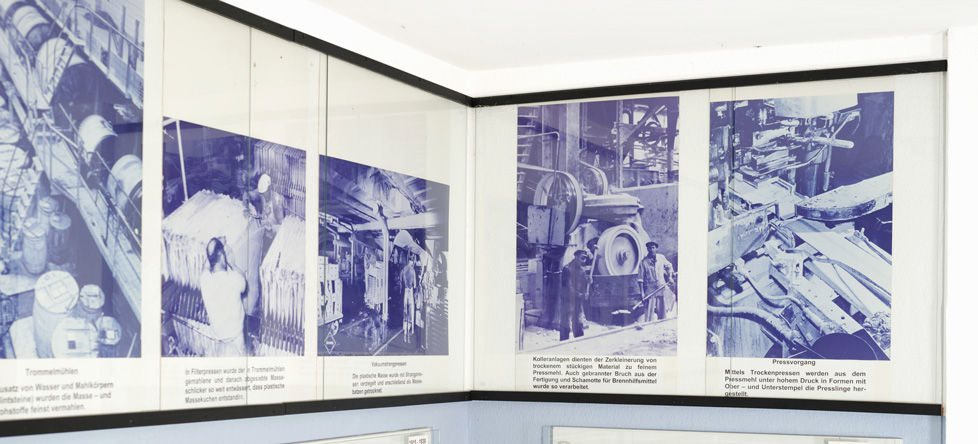

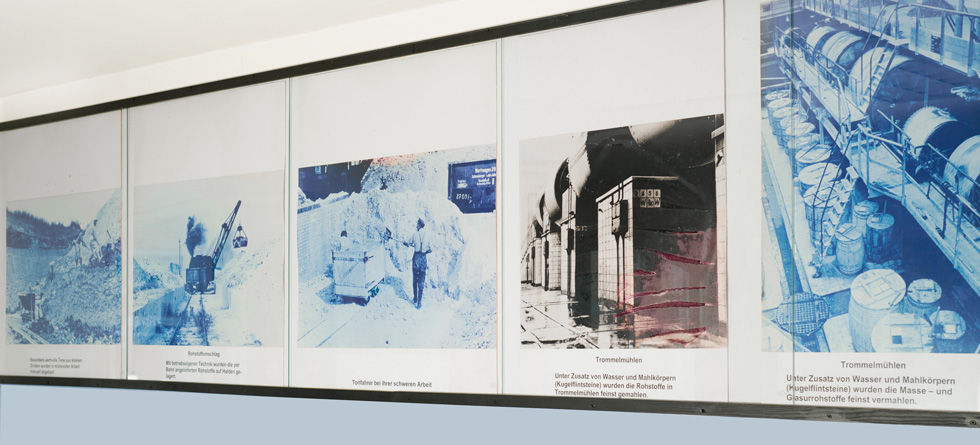
Production of the tile blanks
Industrial tile production required a lot of energy and large amounts of mineral raw materials. Coal for the furnaces and the various “earths” for tile production came to the Boizenburg port by ship, first from England and later also from Saxony. The tracks for Boizenburg’s city railway from the port to the railway station, which opened in 1889, were quickly connected to the new factory premises with a track switch. Now the plant railway brought the material from the port to the plant, where a crane unloaded the different types of earth to various heaps – also called hocks. Here they were stored for at least a year so that lumps were broken apart by frost. Then the clay haulers used shovels to fill a trolley with the appropriate amount of the earth according to the formulas. From the trolley, the mixture was discharged into dolly tubs at ground level. Water was added, followed by mechanical stirring and sifting until a milky mass was formed. This was pumped into the tumbling mill. Flint pebbles, mostly collected on the Baltic Sea, did the subsequent “finishing work” in the tumbling mill, liquefying the mass before it was poured into the filter presses. Moisture was removed from the mass by pressing it in linen cloths stretched over wooden frames. The resulting press cakes were pressed into sections that were then cut into blocks and dried, usually between the tunnel kilns. It was hard physical labour with a great deal of dust and major temperature fluctuations. Subsequently the blocks were coarsely ground in the edge mill and processed into press powder in a pulveriser. This was pressed into blanks and the manufacturer’s identification was applied to the back. The blanks were sorted into heat-resistant caskets and fed into the tunnel kiln for an initial biscuit firing. A fired tile blank is called a biscuit. The glaze was applied to these, initially by hand, later by dipping, spraying or casting. A second, final firing followed before the finished tiles were packaged and shipped all over the world from the Boizenburg port.